AQL signifie « Acceptable Quality Level« , niveau de qualité acceptable en français. Il s’agit d’une méthode d’échantillonnage aléatoire.
La norme AQL permet d’obtenir une bonne vue d’ensemble du niveau de qualité sans avoir à inspecter 100 % de la production. Bien qu’elle implique une méthode complexe de statistiques pour l’échantillonnage, elle offre essentiellement un niveau de vérification optimisé par nombre défini de pièces vérifiées.
Les tableaux AQL permettent également de déterminer le nombre maximum de pièces non conformes pour trois types de défauts différents, classés selon la gravité des défauts constatés.
Généralement, ces défauts peuvent être :
- Critiques : Le produit est dangereux ou présente un risque pour l’utilisateur final et/ou contrevient aux réglementations obligatoires.
- Majeurs : L’utilisation du produit est affectée, et/ou les défauts sont suffisamment perceptibles pour nuire à la commercialisation ou à la vendabilité du produit.
- Mineurs : Ici, la vendabilité n’est pas directement compromise, mais ce type de défauts doit être mentionné, compté et limité.
Comment cela fonctionne
Cela commence par deux tableaux déjà remplis, A et B. Le tableau A détermine une lettre en fonction de deux facteurs :
- La quantité de production
- Le niveau d’inspection qui sera appliqué
Niveau I : C’est le niveau d’inspection le moins strict. Il implique une taille d’échantillon plus petite, donc moins de pièces sont vérifiées. Ce niveau est souvent utilisé lorsque la confiance dans la qualité du fournisseur est élevée ou lorsque les risques pour l’acheteur sont faibles.
Niveau II : C’est le niveau standard, le plus couramment utilisé dans l’industrie. La taille de l’échantillon est plus grande qu’au niveau I, ce qui offre une meilleure représentativité de la qualité globale de la production. C’est un compromis entre précision et coût/effort d’inspection.
Niveau III : C’est le niveau d’inspection le plus strict. La taille de l’échantillon est encore plus grande, ce qui signifie que davantage de pièces sont vérifiées. Ce niveau est utilisé lorsque la qualité est critique, que le produit a une valeur élevée, ou que des problèmes de qualité ont été détectés lors d’inspections précédentes.
Contexte d’utilisation
Niveau I : Utilisé pour des produits à faible risque ou lorsque le fournisseur a un historique de qualité fiable. Par exemple, après plusieurs lots conformes, un acheteur peut réduire le niveau d’inspection pour économiser du temps et des coûts.
Niveau II : C’est le niveau par défaut, adapté à la plupart des situations, en particulier pour les produits de consommation courante où un équilibre entre coût et précision est nécessaire.
Niveau III : Utilisé dans des situations où la qualité est cruciale, comme pour des produits de haute valeur, des produits liés à la sécurité (médicaux, automobiles, etc.), ou si le fournisseur a un historique de non-conformité. Cela augmente les chances de détecter des défauts.
Impact sur le risque acheteur/fournisseur
Avec un niveau I, le risque pour l’acheteur est plus élevé, car une petite taille d’échantillon peut ne pas détecter des défauts présents dans le lot (risque d’accepter un lot défectueux). Cependant, cela réduit le risque pour le fournisseur de voir un lot acceptable rejeté.Avec un niveau III, le risque pour l’acheteur diminue, car une inspection plus approfondie est plus susceptible de détecter des défauts. En revanche, cela augmente le risque pour le fournisseur, car un plus grand échantillon peut révéler des défauts qui auraient pu passer inaperçus avec un échantillon plus petit.
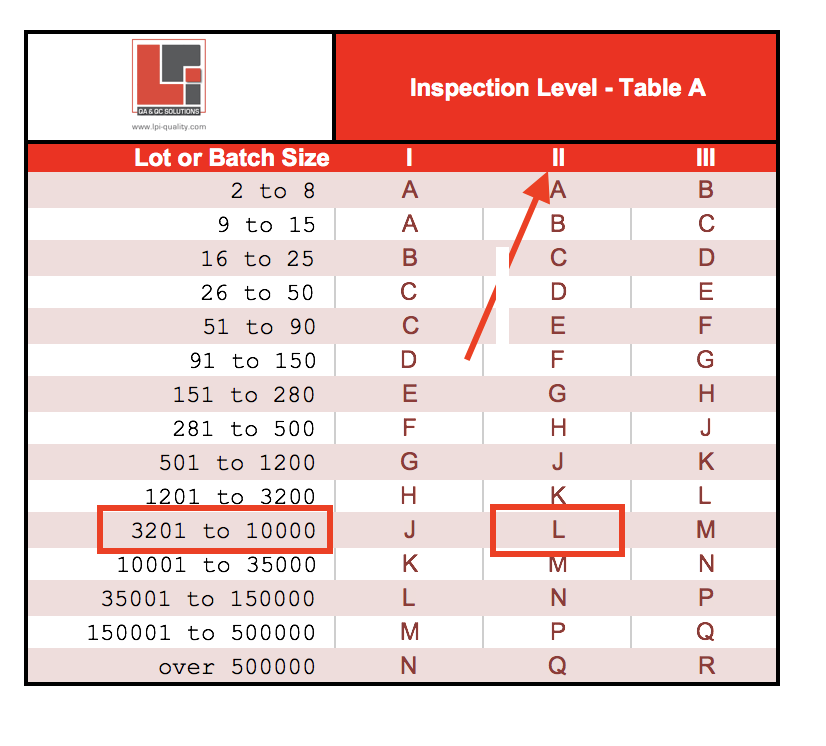
Example :
Imaginons une production (taille du lot ou batch) de 5 000 pièces. On peut voir ici qu’au niveau standard II, la lettre correspondante est L.
Une fois la lettre connue, on peut utiliser le tableau B. On constate, dans la colonne de gauche, que pour la lettre L, la taille de l’échantillon correspondante est de 200 pièces.
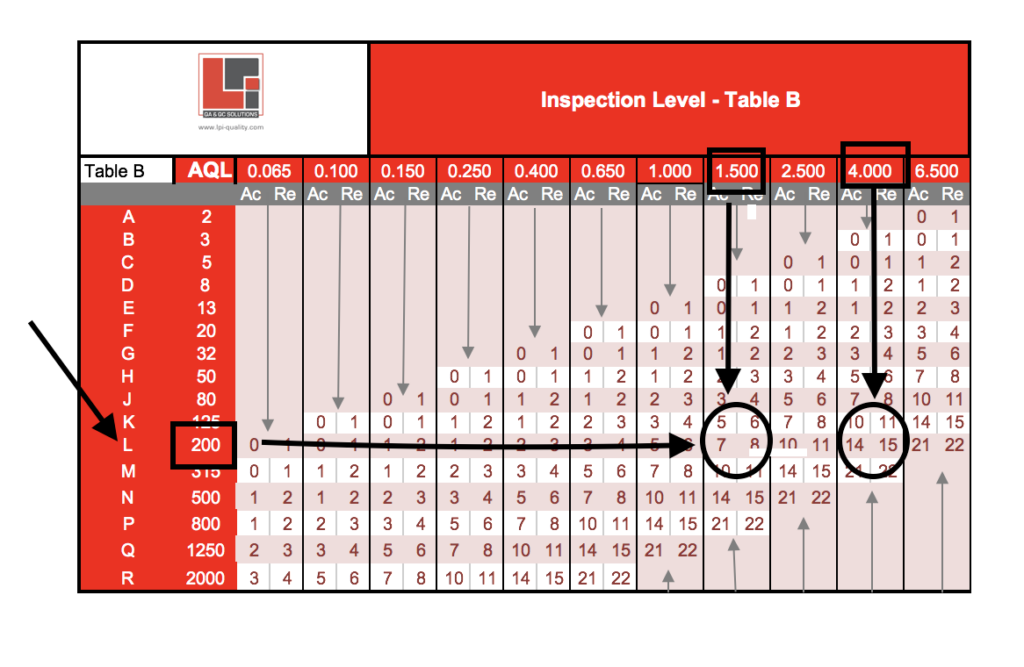
- Ac : Nombre d’acceptation
- Re : Nombre de rejet
Ensuite, on regarde les chiffres de cette ligne. Ils correspondent aux différents pourcentages pour les défauts critiques, majeurs et mineurs. Dans cet exemple, supposons que le client achète des emballages de produits de haute valeur. Il fixe la limite à 0 défaut critique, 1,5 % de défauts majeurs et 4 % de défauts mineurs.
Sur cette base, on peut déterminer que pour une taille d’échantillon de 200 pièces avec un AQL de 1,5 :
- Jusqu’à 7 pièces défectueuses en défaut majeur et 14 en défaut mineur représentent un « nombre acceptable ».
- 8 pièces défectueuses ou plus en défaut majeur ou 15 en défaut mineur entraînent l’échec de l’échantillon à l’inspection. Ainsi, tous les produits du lot seront rejetés. En d’autres termes, pour respecter l’AQL 1,5, pas plus de 7 unités de cet échantillon ne doivent échouer à l’inspection.
Dans cet exemple, vous avez peut-être remarqué que 1,5 % de 200 ne donne pas 7. C’est là que les statistiques entrent en jeu. Comme nous ne vérifions qu’une petite partie de la production, il est toujours possible que, dans cet échantillon particulier, nous trouvions 6 défauts alors que la proportion réelle de défauts dans la production totale (taille totale du lot) ne dépasse pas 1,5 %.
Risque du fournisseur vs Risque de l’acheteur
Pour les fournisseurs, il existe un risque potentiel que leur production soit rejetée bien qu’elle respecte le niveau de qualité demandé. Cependant, statistiquement, la probabilité de trouver 8 défauts ou plus sur 200 pièces inspectées est assez faible si le pourcentage total de pièces défectueuses est inférieur à 1,5 %.
D’un autre côté, il existe également un risque que l’inspection basée sur l’AQL déclare l’échantillon « conforme », alors qu’en réalité, la proportion de défauts dans l’échantillon inspecté est proportionnellement plus faible que dans l’ensemble de la production. C’est ce qu’on appelle le risque de l’acheteur. Il ne faut pas le sous-estimer.
La norme AQL favorise les fournisseurs, car elle prend en compte leur risque de manière plus extensive que celui de l’acheteur. Par conséquent, lorsqu’un résultat AQL est échoué, les clients ont toute la légitimité pour demander à leurs fournisseurs de retravailler la production et de payer pour une réinspection.
Niveau d’inspection et sévérité
Les acheteurs devraient tirer pleinement parti des outils à leur disposition pour améliorer la précision des inspections. Tout d’abord, les niveaux (I, II et III) devraient varier en fonction de la confiance de l’acheteur envers son fabricant.
Plus la taille de l’échantillon est grande, plus la marge d’erreur diminue. Le résultat de l’inspection devrait refléter plus précisément la qualité globale de la production à mesure que l’on monte dans les niveaux (le niveau III étant le plus précis).
Ainsi, si, après plusieurs commandes, vous constatez que la qualité de votre fournisseur est généralement bonne, vous pourriez envisager de réduire la taille de l’échantillon au niveau I. À l’inverse, si le dernier rapport montre que la production n’a pas répondu aux exigences, il est logique d’augmenter le contrôle au niveau III.
Quant à la sévérité, pour les produits de consommation courants, la norme tolère 0 défaut critique, 2,5 % de défauts majeurs et 4 % de défauts mineurs. L’acheteur peut choisir un niveau différent en fonction de l’industrie, de la valeur du produit et du type d’utilisateurs finaux. Il est essentiel de communiquer sur ces niveaux AQL avec l’usine avant de passer une commande, ainsi que de les mentionner dans le bon de commande ou le contrat.
Découvrez notre calculateur AQL.